Even with generations of accumulated knowledge, farming continues to require innovation and informed decision making. Thanks to a plethora of scientific discoveries and inventions, farmers are now better at their jobs than ever before.
Basics of Factory and Farm Automation
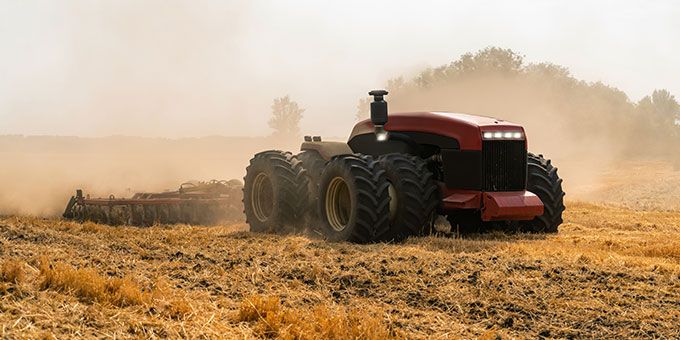
Article from | CIMON Inc.
Understanding the Basics of Factory and Farm Automation
Agriculture is arguably the cornerstone of human civilization. By producing food in large, predictable quantities, people are able to specialize and focus on other jobs. Even with generations of accumulated knowledge, farming continues to require innovation and informed decision making. Thanks to a plethora of scientific discoveries and inventions, farmers are now better at their jobs than ever before.
In a similar fashion, the production of goods has changed dramatically over the past few centuries. Consumer products are not only more complex in their design; they are also manufactured using a higher level of precision and detail. With the rise of advertising, digital commerce, and logistics, companies are able to contend with competitors around the globe. For the consumer, this has resulted in greater accessibility to goods, higher quality, and lower prices.
Despite this success, there is still a very real need for improvement. As the population rises and standards of living increase, farms will need to become ever-more efficient. Likewise, factories will need to produce more intricate products and become more flexible to match evolving consumer expectations. All this must be done without expanding land usage, and without contributing to climate change.
Smart Farms and Factories
The latest efforts to achieve this focus on making better use of data and incorporating more advanced machinery. The key to this is automation, whereby work that once required intensive manual labor can instead be performed by programmable equipment. A smart farm or smart factory is one that makes the most of the information and technology available to it by embracing automated workflows. When done well, these changes lead to vastly improved efficiency, productivity, and ease of maintenance.
While farm and factory automation are different in many respects, they share many of the same challenges and can often benefit from the same solutions. For example, both involve large-scale, repetitive, and sometimes dangerous physical tasks. As a result, heavy-duty machinery has been extremely beneficial in both applications.
Still, farming presents unique difficulties which are just beginning to see automated solutions. Notably, most farms are outdoors, and thus subject to unpredictable events and environmental conditions. Inside a factory, the temperature, light level, moisture, and air quality can all be closely regulated. Outdoor farms have no such luxury, so the focus is instead on being prepared and making accurate predictions. On top of this, the physical shape and appearance of plants cannot be controlled in the same way that an assembly line’s components can. Thus, a machine that works well for one tree, crop, or farm may completely fail for another.
Nevertheless, farmers have been successful for thousands of years. In automation and in any other endeavor, the goal is not to perfectly control and optimize, but to make incremental progress by identifying areas for growth. With that in mind, we’ll look at just a few emerging technologies which are set to shape farming in the coming decades. These changes will significantly improve the lives of farmers and the general population alike.
The Internet of Things
In a traditional industrial setting, natural variation is seen as a hurdle to overcome. Processes are performed in large batches with identical, precision-machined instruments. While this approach is efficient, it does not often reflect the real world. Ultimately, the inputs for any production line come from natural resources, and these are rarely as uniform as one might hope.
In order for a machine to adjust to such variation, a dynamic yet accurate description of the input must be given. In the case of a log being cut for wood, this might mean measuring the thickness along its length as well as identifying knots, holes, and other irregularities. Without this information, the cutting machine would need to treat every log the same, which would waste valuable material. By handling ingredients of different shapes and sizes, a factory can not only save material, but also make use of lower-quality sources without sacrificing the product quality.
Likewise, a process further down the line should be able to react to changing output. If too many boards of a certain size are being produced, the factory-wide behavior could be adjusted to compensate. This boils down to collecting data at the source and delivering it to the machinery and experts who need it. In practice, this means installing a network of physical sensors, typically connected over a wireless or Ethernet connection; these networks are collectively referred to as the Internet of Things.
In agriculture, this kind of useful data is effectively unlimited. A skilled farmer can ascertain a crop’s age, health, and much more just by looking at it, but most farms are far too large for every plant to receive this level of attention. Instead, most farms rely on statistical measurements and enforced uniformity. No two plants or patches of soil are alike though, meaning many plants will be over- or under-tended. Given low-level sensor data, farms can combat this problem by focusing on crops that need the most attention. Watering, fertilization, and pest treatment can then be handled at a much smaller scale, with much greater accuracy and timeliness.
Not all of this information needs to be used immediately. By storing and analyzing past data, operators can make informed decisions about which strategies are effective, how employees and machinery are performing, and what to invest in going forward. Data collected on one farm may also be valuable to other farmers, weather services, or connected supply chains. With a bit of collaboration, the possibilities are nearly endless.
Machine Vision
Some data is fairly straightforward to measure and utilize. Moisture level, for example, can be treated as a single number that shows how much water a given patch of land needs. In comparison, abstract concepts like the size, shape, or color of a plant are much more difficult for machines to make use of. The practice of extracting such information using cameras, lasers, or other geometric sensors is called machine vision.
A typical machine vision system involves a visual sensor, a computer to process the images, and some physical machinery that makes use of the data. Actions can be as straightforward as scanning and storing a barcode or as sophisticated as removing weeds with a robot while leaving crops intact. Depending on what needs to be done, the internal representation of the object at hand can be 1D, 2D, 3D, or something more abstract.
Common examples of 1D machine vision include scanning barcodes and measuring distances. While the overall image may be two-dimensional, only one line is scanned at a time. 2D imaging uses a more traditional photographic image, and may be used for QR codes or working with image-based neural networks. 3D imaging involves scanning and generating a realistic model of an object. A pulsed light source quickly measures distances to create a set of 3D positions called a point cloud. Multiple point clouds can even be combined to form a 360-degree representation.
When properly automated, machine vision allows industrial equipment to work flexibly, taking in inputs with irregular properties and adjusting as needed. On top of this, the kind and amount of detail far exceeds what a human eye can detect. Combined with machine learning and specialized computers, an industrial imaging system can be trained to recognize abstract patterns hundreds or thousands of times per second.
Furthermore, machine imaging is not limited to the visible spectrum. The infrared, ultraviolet, and even auditory ranges can provide information that normally goes unused. Some systems take advantage of this by marking seeds with an invisible fluorescent dye. Weeds lacking the dye can then be identified and safely removed.
One especially impressive example of machine vision is an automatic apple-picking robot designed by Abundant Robotics. Using a vacuum attached to a robotic arm, the robot automatically finds and picks ripe apples, then gently places them into a bin. New Zealand-based company T&G Global has already used the robot to harvest several of their orchards, with plans to expand in the future.
Picking fruit is one of the most difficult and labor-intensive tasks in farming. As the availability and affordability of workers declines, this technology will help keep orchards viable. In the future, we are likely to see robots capable of picking fruits and vegetables of any variety.
Autonomous Vehicles and Drones
An intrinsic difficulty of working with farmland is the sheer scale of operation. Tending a field takes many hours of planning and manual labor, and this scales directly with size. Many of the associated jobs—especially those involving large machinery—require little meaningful human interaction. These jobs are especially well-suited for automation.
Recent years have seen the rise of autonomous tractors. These machines can operate without a driver using predefined paths or remote control. Farmers can monitor progress from a separate location and take over when needed. In addition, autonomous tractors can be faster, more efficient, and more cost-effective because there is no need to accommodate a driver.
To help with monitoring, aerial drones can perform photography and other kinds of imaging. Some cameras are even sensitive enough to zoom in on individual leaves, making note of pests, disease, or other irregularities.
Drones can also be equipped with specialized equipment for spraying chemicals or planting saplings. Because drones can stay closer to the ground than traditional airplanes, they can spread pesticides more efficiently and avoid harming the surrounding environment.
Most importantly, autonomous vehicles can be scaled to match any size of land simply by increasing their number. While one might say the same of manual labor, most agricultural jobs are seasonal, meaning farmers must find, hire, and relocate workers over short timeframes. In contrast, a machine can be used year-round at a moment’s notice.
SCADA: an Overview
To help oversee a farm or factory, the most common practice is to use a supervisory control and data acquisition (SCADA) solution. SCADA is a type of industrial management tool that provides a customizable interface, data collection, reports, alarms, and more. Nearly any piece of equipment can be connected to a SCADA system, giving the operator both low-level and high-level control over the entire operation.
SCADA and other control software is essential for keeping track of progress and triggering actions. By making everything accessible from a single computer, supervisors can spend less time going from site to site and more time on planning and analysis.
This is far from a complete list of the innovations that agriculture and industry have seen in recent years. We have not covered vertical farming, precision seeding, plant genomics, or chemical fertilizers, all of which will be immensely important going forward.
The technologies presented in this article are designed to work together as a cohesive whole, and that is what makes them so powerful. Although the individual processes may change, the focus should always be on achieving an overarching goal. For this reason, the next era of industry will be shaped by rising access to information across devices and projects.
CIMON makes industrial automation products for general manufacturing, automotive assembly, agriculture, building automation, chemical plants, pharmaceutical, food & beverage, bottling, packaging, marine applications, mining, oil & gas, water treatment & wastewater, power & utilities, pulp & paper production, and transportation & tolls. Our products include UltimateAccess SCADA software, Xpanel HMI and XpanelDesigner software, CIMON PLC and CICON software (for PLC programming), and a line of Industrial PCs, some with SCADA software included. We are dedicated to the future of automation, with a focus on helping newer engineers, integrators, and OEMs become successful by collaborating with, assisting, and educating them to solve problems.
The content & opinions in this article are the author’s and do not necessarily represent the views of AgriTechTomorrow
Comments (0)
This post does not have any comments. Be the first to leave a comment below.
Featured Product
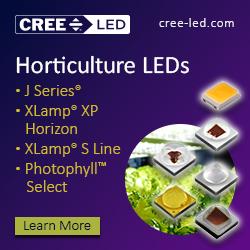