The key to growth in the Indoor Agriculture industry is to compete with traditional farming. That requires maximizing yields efficiently and reducing waste. We see the potential of being able to automate from seed to harvest to packaging to grocer.
Bridging the Gap from Farming to Today’s Highly Efficient Manufacturing Methods

Q&A with Ken Bylo, Executive V.P. / Partner | PolyFlex Products Inc.
Tell us about yourself and PolyFlex Products.
PolyFlex Products is a manufacturing company that focuses on the design, engineering and manufacturing of plastic products for industry.
How does PolyFlex fit into the Agriculture industry?
PolyFlex is the link that brings the new ideas of indoor agriculture to reality. Our customers are experts in growing but not necessarily experts in how to get a product produced that will satisfy their goals. We are that resource.
What problems can PolyFlex solve for growers?
PolyFlex has a long history within manufacturing sectors that helps our customers through each stage of their process. From material handling, to shipping, to integrating automation, PolyFlex can help. The reality is that the indoor agricultural industry is evolving into manufacturing. In any manufacturing environment it must be cost effective and efficient. We want to help bridge the gap from farming to today’s highly efficient manufacturing methods. One other key concern we see in this industry is retail packaging. There is a strong push to remove single use packaging. We believe that there is a solution to go from harvest to the grocery or consumer using a returnable pack and significantly reduce costs and waste.
What expertise and technology from other industries transfers into the agriculture industry?
Rapid Prototyping
Everything we do can be adopted to the AG Industry. Robotics, automation, ergonomics, recycling, product handling, environmentally friendly materials, returnable packaging, plastic replacement for metals……. The list can go on.
Share the process of developing new products to support new growing technologies?
PolyFlex uses what we refer to as a PDT group or a Product Development Team. We meet with the customer, gather all of the necessary data. The intent is to extract as much information to develop the most effective solution. We often interact with all stakeholders both internally and externally. Everyone’s voice will be heard. This eliminates last minute surprises. A typical project generally adheres to the following path: data gathering, engineering/design, prototyping, trial, production tooling, production, implementation.
What is the PolyFlex Products Circular Lifecycle?
Times have changed, there is a concerted effort to recycle. Nearly all of our products are 100% recyclable. PolyFlex has adopted a Circular Lifecycle approach in our design. This may be of particular interest to the Indoor Ag Industry. There is an obvious green initiative that this approach serves however there is still value in residual, original and left-over materials once they have served their intended usefulness. Reclaiming the usable portion of the production material and recycling it to be used again in your facility can reduce material costs and have a significant positive impact on the environment.
Environmental savings include:
- Reduction of greenhouse gas emissions
- Reduction of electricity usage
- Reduction of petroleum usage
- Reduction of landfill waste
We effectively manage the circular product lifecycle. Some customers partner with us to remove their obsolete plastics; others participate in the full circular product lifecycle by sending us their used industrial plastics to be recycled and reintroduced into new product production.
Download our Recycling/Circular Product Lifecycle for Plastics Case Study
https://polyflexpro.com/circular-product-lifecycle/
Where and how do you see manufacturing automation playing a critical role in indoor growing in 5-10 years?
The key to growth in the Indoor Agriculture industry is to compete with traditional farming. That requires maximizing yields efficiently and reducing waste. We see the potential of being able to automate from seed to harvest to packaging to grocer.
About Ken Bylo
Ken Bylo, Executive V.P. / Partner, PolyFlex Products Inc. has 30+ years in manufacturing, plastics, tooling, engineering, automation, robotics and recycling.
The content & opinions in this article are the author’s and do not necessarily represent the views of AgriTechTomorrow
Comments (0)
This post does not have any comments. Be the first to leave a comment below.
Featured Product
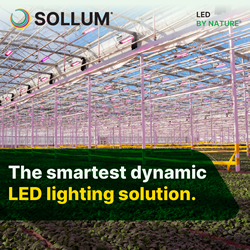