JPI Farms from Canada grows cucumbers and bell peppers. Innovative tools are constantly being looked at to simplify and improve processes inside the greenhouse.
‘Autonomous Growing makes me sleep better as a head grower’
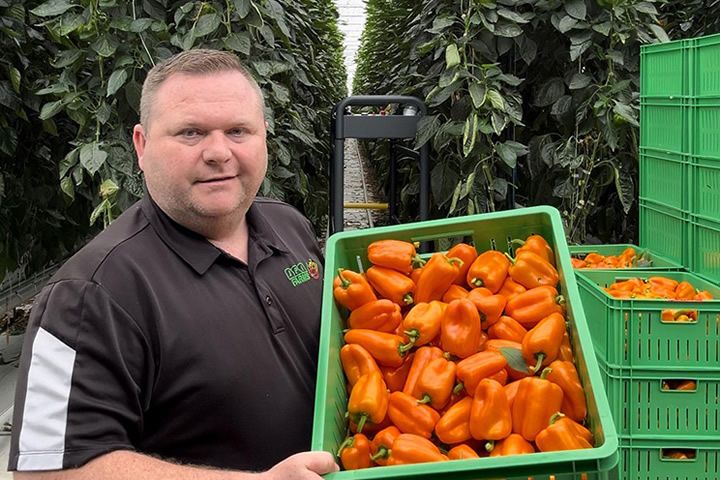
Case Study from | Blue Radix
JPI Farms from Canada grows cucumbers and bell peppers. Innovative tools are constantly being looked at to simplify and improve processes inside the greenhouse. Last year, JPI Farms started with Autonomous Growing for the first time, this year Blue Radix's Crop Controller is used on almost 22 hectares of bell peppers.
JPI Farms was founded in 2002 by their father but is operated today by John Giesbrecht and his brothers Peter and Isaac. It’s a real family business, says John Giesbrecht. Within the company he is the head grower. “For me, growing cucumbers and bell peppers is not just a job, it is a passion. I love what I do and our goal is to offer the best and healthiest products to consumers.”
More responsibilities
The company has approximately 7 hectares of mini cucumbers and around 22 hectares of red, yellow and orange bell peppers. JPI Farms also takes care of the sorting and packaging of the products itself. “We have invested in robots to deliver a uniform product and to ensure that the cucumbers and bell peppers are beautifully packed to be sold in Canada and the United States.” The biggest challenge for the company is labor, Giesbrecht indicates. “It is becoming increasingly difficult to find enough workers. Working in the greenhouse is not attractive enough for many people. Moreover, there are many horticultural companies in the area and most of them continue to grow. It is therefore very easy for people to switch to another company. As a result, we have to do the work with fewer and fewer people and our employees are also given more and more responsibilities. But there are limits to that.”
It was the main reason for Giesbrecht to seriously look at the possibilities of Autonomous Growing. He came into contact with Blue Radix through SEF, the contractor who realized the expansion of JPI Farms. “We started a trial with Crop Controller in 2023 and I quickly noticed the benefits. The system ensured that many tasks in the greenhouse were taken over, which freed us up for other things. That is why we have decided this season to control the entire bell pepper area with Crop Controller.”
Giesbrecht had not worked with AI before, he says. “Computers can do a lot these days, but I initially found it difficult to let things go. When we first started working with Crop Controller, I still wanted to be involved in everything. But that’s no longer possible. The company has become too big and the cultivation too complex. Flipping that switch inside my head was perhaps the most important step. I said to myself: you need help, you're getting it now, so you must let it go. And to be completely honest, that decision felt like a huge relief.”
Comfortable to work with
What helped was that Giesbrecht soon noticed that Crop Controller could handle the work effortlessly. “In the beginning I kept a close eye on everything, but the system really surprised me in a positive way. Moreover, I received all the support from Blue Radix, which made it comfortable for me to work with Crop Controller. Every week we have a video call with our Autonomous Greenhouse Manager to catch up and if something comes up I can quickly and easily send a text message to solve things. Knowing that you are not alone gives you a lot of peace.”
Giesbrecht also notes that it is a simple system to work with. “You don't need extensive digital knowledge to get started. That doesn't mean everything went perfectly right away. There are always glitches when you're starting something new. Every company is different, every crop is different, every grower is different. So, the system must adapt to the situation and your personal preferences. That's part of it. But I noticed that it gradually became easier for me to let things go and that I gained more and more confidence in the system.” Giesbrecht has to monitor and follow three types of cucumbers and three types of bell peppers during all phases of cultivation. “Previously, I wrote down everything that needed to be done, but after working with Crop Controller for a while, I noticed that I wrote down less and less. That was a signal to me that the system really is of added value and offers a lot of support.”
Stress reliever
The good experiences with Autonomous Growing during the trial period led to Crop Controller being rolled out to the entire 22 hectares of bell peppers this season. But what has the system actually brought Giesbrecht as a head grower? “Some people say it has led to extra yield or better quality, but I don't think that's really the most important thing. For me, Crop Controller has mainly proven to be a stress reliever. Knowing that you are not alone, that the crop is monitored and that you can trust everything goes as planned, that is the most valuable thing about all of this for me. A weight has really been lifted from my shoulders, which makes me feel like we can handle all the work in the greenhouse again.”
At the same time, Giesbrecht hopes that the implementation of Crop Controller will ensure that the company's employees are kept on board. “Everyone makes mistakes, I am the king of that. But people often feel attacked or guilty when they make mistakes. Now that we have a system that reduces the chance of errors, this will also take some pressure off our employees.”
Constantly learning
If someone had asked Giesbrecht two years ago what he thought of Autonomous Growing, he would not have responded positively. “That's how I felt at the time, I didn't believe that a computer was able to do what I do. But my view on Autonomous Growing has really changed. Now I see the opportunities for our company, also knowing that the technology will get even better in the next years. The system is constantly learning and new features are being added. I am really looking forward to the Autonomous Irrigation Control, because water management is one of the most important parts of my job. I am very curious what this new tool of Crop Controller will bring us. Just as I hope for additions regarding screening and fogging systems in the future. All these developments ultimately ensure that I will sleep better as a head grower.”
The content & opinions in this article are the author’s and do not necessarily represent the views of AgriTechTomorrow
Comments (0)
This post does not have any comments. Be the first to leave a comment below.
Featured Product
