Prince Edward Island’s warehouses look distinctly different than they did 10 years ago. Many farmers in this region have introduced raw material inspection systems as an added safety precaution.
Farmers Crack Down on Finding ‘Needle in the Potato-sack’
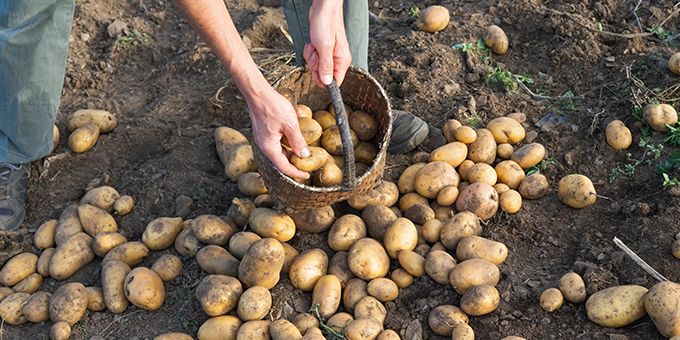
Case Study from | Fortress Technology
Potatoes are one of the world’s most versatile, main food crops and demand never drops. French fries, potato chips and table potatoes are a staple in most households. With the annual farm gate value of potato production in North America exceeding USD 4.5 billion and generating more than USD 100 billion for the economy, it’s no wonder that farmers are prioritizing the implementation of inspection solutions to safeguard their reputations and livelihoods.
Prince Edward Island’s warehouses look distinctly different than they did 10 years ago. Many farmers in this region have introduced raw material inspection systems as an added safety precaution. With 89,000 acres of land accounting for 25% of Canada’s potato production, ensuring that their crops are free of metal contaminants is essential to these thriving farms.
Introducing this level of scrutiny is not unfounded. In October 2014, potato processors suffered a serious industry blow – product tampering. Needles were discovered in PEI potatoes, resulting in a nationwide recall of nearly one million pounds of produce. Despite this setback, business operations resumed. The following harvest, more needles started to appear on other farms.
“Several years ago, steel needles and other sharp metal objects were detected in Prince Edward Island (PEI) potatoes at processing plants and in bags sold throughout Atlantic Canada. Although no foreign objects were present in our customer’s produce, they were keen to prevent such an incident occurring at their own plant and to reassure their extensive supplier base. This led to the investment of three robust industrial-sized metal detectors from Fortress Technology, each inspecting 140,000 pounds of potatoes every hour,” explains Fortress Technology’s Regional Sales Manager and food safety specialist, Eric Garr.
THIS IS NOT A DRILL!
These days, food safety is driven by retailers and legislation, and most notably, prolific consumer awareness. The probability of a company going viral on social media for food contamination is at an all-time high. “This type of brand-damage can quite literally destroy a business overnight,” cautions Eric.
For instance, without upstream inspection, a potato containing a needle could unknowingly be thinly sliced into potato chips. The subsequent metal fragments may be too small for even the most sensitive downstream metal inspection systems to detect.
And it’s not just needles. A soda can casually discarded in a crop field, machinery nuts and bolts, or wire fencing blown down in a storm, can all be turned into the smallest metal fragments by powerful harvesters. These can, easily disperse and imbed contaminants into crops.
Addressing these fears directly, Fortress Technology designed and manufactured a customized Phantom metal detection system. Three industrial-sized Bulk Potato Slider Detector Systems were swiftly installed by Fortress at a prominent East Coast crop processor to handle loose, rolling potatoes. To this day, they continue to play an important role in guaranteeing high standards across the potato supply chain and provide valuable assurance to major retailers.
MACHINES WITH GRIT
When coming up with the robust design, Fortress was mindful that potatoes have a number of product attributes that could affect the accuracy of the metal detectors. Eric elaborates: “The potatoes are typically washed and wet. They are neither super clean or dry, and they come in all different sizes.” These factors can impact a metal detector’s ability to distinguish between the potatoes and any metal contaminants introduced, leading to false signals and consequently, wasted produce.
To ensure the potatoes were run at the highest performance level, Fortress engineered a special VLF (very low frequency) coil. This allows all potatoes to appear as dry products on the machine, essentially ignoring the product effect caused by soil, grit and moisture.
Another essential feature designed for harsh, rigorous production environments is the BSH rugged casing. This helps to provide better stability and metal detector performance for when rolling potatoes collide with the sides of the system as they are funneled down the conveyor.
Orientation effect, especially when trying to detect long, thin needles, was another added challenge Fortress had to resolve when designing the system. Most of the time, these contaminants will be imbedded within the potato or root vegetable. Detecting any fragments will depend entirely on the direction that a bouncing potato is passing through the metal detector. In one orientation, the signal for the needle may be huge. But if turned 90 degrees, the needle may pass through the metal detector’s electromagnetic field undetected with little to no disturbance.
To combat this, Fortress designed the metal detector without a traditional belt system. Instead they opted for a rolling-system, recognizing that it provides a stronger signal than stagnant objects. “The potatoes roll through the metal detector to limit the chance that a needle misses detection due to orientation effect,” expands Eric. The technique worked remarkably well in all test cases, with the customized Phantom metal detection unit reporting minimal false positives and superior accuracy and metal detection sensitivity.
NO BELT, NO PROBLEM
Special consideration was also given when addressing rejects and warehouse floorspace. For the Canadian potato grower, a reject system that would align with the other robust design features was required. Eric continues: “It was a tight space with fast product rolling through. We couldn’t account for the placement of the potatoes as they passed through the metal detectors at speed. The benefit of the roll-through design was that there was no belt. Ultimately allowing us to introduce a flap that meant any contaminated product would be expelled down to the reject area below.”
A simple conveyor with a low-maintenance UHMW slider bed was integrated alongside the farmers existing cleaning and grading systems, resulting in an optimized and cost-effective solution.
FIELD TO FORK ASSURANCE
It’s increasingly clear that the task of contamination control is no longer reserved for food processors; it stretches right up the supply chain. With the Food Safety Modernization Act (FSMA) shifting focus from analyzing hazards to preventing them, contaminant detection from farm right through to fork is essential to securing new business deals and guaranteeing the delivery of consumer-safe products.
Safety in the fast-evolving food sector places heavy emphasis now on shared responsibility, notes Eric. Upstream inspection after harvesting and before processing is now widely regarded as best practice.
Globally, farmers face multiple challenges every year, from floods and droughts to poor harvests, fluctuating energy costs and crop damage. “Although product tampering is extremely rare, in the last decade Fortress has observed a large uplift in inquiries from root vegetable and potato farmers and bulk processors for robust gravity and conveyor metal detection systems. These can help to prevent future adulteration and contamination events from causing potentially catastrophic damage to brand reputations,” ends Eric.
The content & opinions in this article are the author’s and do not necessarily represent the views of AgriTechTomorrow
Comments (0)
This post does not have any comments. Be the first to leave a comment below.
Featured Product
