Pleora’s Visual Inspection System Helps Ensure Brand Quality for Dairy Distillery
Pleora Technologies today announced that Dairy Distillery, a spirits producer that combines artisanal distilling techniques with a scientific process to transform milk into vodka, is using its Visual Inspection System to help maintain brand quality standards and reduce errors that increase operating costs and slow production.
Dairy Distillery has pioneered a unique process that uses milk permeate, a byproduct left over after cream, fat, and proteins have been removed from whole milk for use in products such as butter, ice cream, and yogurt, to create a clean and pure spirit. Previously, milk permeate was considered a waste product that had to be disposed of at a cost to the farmer. Founded in 2018, the Almonte, Ontario based business now ships over 100,000 bottles of its flagship Vodkow Vodka and cream liquors to global customers. In 2020, the distillery became a major supplier of hand sanitizer to Ottawa hospitals and vaccination clinics as part of the fight against coronavirus.
Operating in a highly competitive market, brand appearance is a key factor in ensuring consumer shelf appeal. The distillery’s Vodkow bottle integrates machine-placed labels with a distinctive emblem that is hand-placed by a human operator. The operator needs to accurately align the emblem with brand elements on the main label to ensure a consistent and appealing shelf display.
“We’re a world-class product, and our packaging needs to look perfect every time,” said Neal McCarten, co-founder and Director of Marketing, Dairy Distillery. “When you say you’re making vodka from milk, it can be a leap of faith for a consumer until they taste the product. Our packaging fashioned after a traditional milk bottle and eye-catching labelling is a real shelf talker that helps a consumer connect with the story behind the product. Consumers often judge what’s inside a bottle based on its appearance.”
To help ensure brand consistency, the distillery uses Pleora’s AI-based Visual Inspection System to add decision-support for manual labelling processes. The camera-based system integrates pre-packaged AI plug-ins that are easily trained on a customer’s unique requirements to visually highlight product differences and deviations for operators and inspectors on a display. The distillery trained the Image Compare plug-in to identify key brand elements on the bottle, with a real-time on-screen image overlay then guiding operators as they manually place the emblem. In addition, the system can be used as a training tool to teach new employees on brand quality standards.
The Visual Inspection System helps the distillery reduce costs and avoid production downtime, as labelling errors can be avoided or detected earlier in the process. As Dairy Distillery seeks to further automate production processes to keep pace with growing consumer demand for its products, it is now investigating ways to use Pleora’s system for quality control (QC) checks for in-production and finished goods.
“As a premium brand, there’s an important human element to our processes – from the distilling to packaging – but technology helps ensure high-quality products consistently go out the door,” said David Geros, Chief Operations Officer, Dairy Distillery. “Packaging errors translate into downtime, slower production, and higher costs. Pleora’s system is simple and easy to use, and helps removes ambiguity and stress for employees. We can check a product and know immediately if the labelling is within tolerance. As a QC tool, the inspection system helps increase our confidence in both our manual and automated processes.”
“Leading manufacturers are deploying our Visual Inspection System and realizing immediate cost and process advantages,” said John Butler, Vice President of Sales & Marketing, Pleora Technologies. “For companies like Dairy Distillery, where brand and packaging play a significant role in consumer choice, our system ensures manual processes are consistent, reliable and repeatable so good products are always on the shelf.”
Pleora’s Visual Inspection System and AI expertise is also being deployed in electronics assembly, packaging, print and consumer goods applications to help ensure end-to-end quality. The company will be demonstrating its AI portfolio, including the Visual Inspection System, “no code” algorithm development platform, and edge processing, at Photonics West 2022, January 22-27 in San Francisco, CA (booth 4322). Pleora will also be hosting a live webinar – Protect Your Business with AI for Visual Inspection – on Wednesday, February 2 at 11 am EST.
About Pleora Technologies
Global manufacturers rely on Pleora’s expertise in AI, real-time sensor connectivity, and rugged networking to shorten time-to-market, reduce risk, and lower costs. Established in 2000, the company serves over 1500 active customers in the industrial automation, medical imaging, and security and defense markets. The company’s latest AI solutions include an intuitive “no code” software platform, edge processing, and camera-based visual inspection system to help manufacturers reduce quality errors. Learn more at pleora.com.
About Dairy Distillery
Dairy Distillery was founded in 2018 with the idea to turn unused milk sugars into world-class spirits. Look for their exceptionally smooth, carbon-neutral Vodkow vodka, and their Vodkow Cream, North America's first lactose-free cream liqueur. Learn more at www.dairydistillery.com/.
Comments (0)
This post does not have any comments. Be the first to leave a comment below.
Featured Product
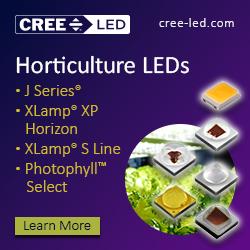