Support for fruit farmers: mobile robots harvest apples
"Both companies are contributing one of their most innovative new developments for automation in fruit growing to this cooperation. With KUKA, we have an absolute specialist with many years of experience and sophisticated know-how in the field of robotics at our side. The result is a practiceoriented collaboration that will provide us with many valuable insights for our next development steps with regard to automation in fruit growing. In the future, we want to test and further develop the interaction of our equipment and exploit synergies, especially with regard to apple cultivation. We are very much looking forward to this," says founder and Managing Director Josef Schmidt of digital workbench gmbh.
Concept study presented to public for the first time at trade fair
Visitors to Agritechnica were able to see the mobile harvesting robot in action. Two KUKA small robots from the KR AGILUS series are mounted on the new Tipard 1800 multi-carrier platform from digital workbench. In a pilot project that has been running since 2020, KUKA is already testing a customized version of the small robot specifically for apple harvesting. With a vacuum suction cup combined with artificial intelligence and vision technology, the extremely maneuverable precision artist has already been successfully used in harvesting test runs.

Compared to a conventional gripper, the vacuum suction cup can distribute the pressure more evenly over the surface of the apple and thus avoid unwanted pressure points. Cameras recognize important parameters such as ripeness, condition and size and, of course, the position of the apple. The carrier platform presented at the trade fair impresses above all with its high performance and almost endless multifunctionality. In addition, the Tipard 1800 takes digitization and automation to a whole new level.
Harvesting robots provide support where skilled workers are lacking
In future, the robot arms will move autonomously across the fruit fields in specific practical projects. The mobile and smart automation solution of the two cooperation partners will then be used where previously harvesting machines with several harvesting assistants were used. "We assume that harvesting robots will be used more and more in the future. The technology still needs to mature for large-scale use and the plantations also need to be planted in such a way that the harvesting robot can work efficiently," says Alois Buchstab, Vice President KUKA Business Development. The aim is to work with digital workbench to develop a robot system that makes the most difficult tasks in agriculture easier. An automatic apple harvesting system that does not damage the crop is an important development in an industry that is dependent on seasonal labor. For KUKA and digital workbench, the key therefore lies in automation.
Comments (0)
This post does not have any comments. Be the first to leave a comment below.
Featured Product
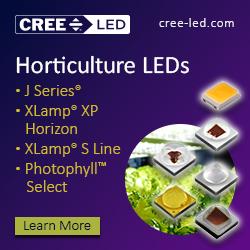