In Singapore, a country with a population of more than 5.5 million on the main island that is just 26 miles wide and 14 miles long, there is a four-story rotating greenhouse, it produces 1 ton of greens every day. Normally, Singapore imports 93% of its produce.
What is Vertical Farming?
Len Calderone for | AgritechTomorrow
Most of us thinking of farming as the growing of crops on the ground. A vertical farm grows plants and produce by stacking the plants. This is accomplished by using growing shelves suspended on a wall or fence, which uses much less space than growing the plants on the ground. Thereby, maximizing the available space.
Most vertical farms are either hydroponic, where plants are grown in a bowl of water containing nutrients, or aeroponics, where the plants’ roots are sprayed with a mist that includes water and the nutrients needed to support plant growth. Neither method requires soil for the plants to grow. Usually artificial grow lights are used, sometimes in conjunction with natural light.
In Singapore, a country with a population of more than 5.5 million on the main island that is just 26 miles wide and 14 miles long, there is a four-story rotating greenhouse, it produces 1 ton of greens every day. Normally, Singapore imports 93% of its produce.
Vertical farming is rather new, but there are some tangible benefits. Because vertical farms can control all of the technology used to grow the produce, crops can be grown year around. If a plant needs a certain amount of humidity and light, a vertical farm can provide what is required. This allows a growing season, normally just a few months long, to be year-round. Another benefit is that a vertical farm doesn’t have bugs and weeds, removing pesticides and other harmful chemicals from the process.
Cold or hot temperatures can affect an entire harvest, while a natural disaster like a flood or hurricane can set a farm back many years. Since most vertical farms are indoors in a controlled environment, weather is no longer an issue. Vertical farms use less water than traditional farms—up to a 70-percent reduction. This is a key benefit in draught prone areas. About 30% of conventional produce is lost to weather and bugs. Vertical farming has much less waste. With global weather patterns becoming more unpredictable, and with global warming being a huge problem, vertical farming could be a workable option.
Another benefit of having a vertical farm is that farms like these within the inner cities reduce the carbon footprint because of the proximity to the consumer, reducing long truck hauls. Because these farms can recycle and use black water in their irrigation systems, drinking water is conserved.
Most produce that we find in the grocery stores are transported some distance, even internationally. This leads to produce with less shelf life. Instead of spending days in transport, produce can be in the hands of a consumer in just hours. Quick deliveries mean less greenhouse gases produced by trucks. I have personally noticed that produce purchased from the grocery stores do not last long after they are brought home.
Instead of 4-6 acres on a conventional farm being used to grow crops, vertical farming uses only one acre of indoor space. This is particularly useful in cities, where outdoor land is limited. Instead of building out, vertical farms allow people to build up. Vertical farms use space that already exists, such as abandoned warehouses or factories. This reduces the need for new construction.
Vertical farmers are looking for ways to minimize their carbon footprint, such as using low energy LED lights, which reduce energy consumption by as much as 80%. They use anaerobic digesters, which use anaerobic bacteria to compost organic material. These can convert waste from the facility, and convert the waste into biogas, which is used as fuel. Rainwater collection and geothermal energy are also utilized.
In Kyoto, Japan a vertical farm is soilless and sunless. They rely on robotics, LEDs, and hydroponics to grow more than 10 million heads of lettuce per year. A former semiconductor factory was converted into an indoor farm. A new facility just came on line and is projected to produce 21,000 heads of lettuce per day. The facility uses new technology for the growing process, eliminating the need for human labor for the stages between seedling and harvest, effectively slashing labor costs. The labor costs were reduced 50% due to full automation of the cultivation process from raising the seedling to harvest.
They developed low-cost LED lighting, which is specific to plant factories. These lights use less energy and are highly efficient, which has helped achieve the goal of cutting power consumption by 30% in the new factory.
A recycling, filtering and sterilization system was developed to recycle 98% of the water used. This system reduces the amount of water required per head of lettuce down to 0.11 per liter.
They use a large area air conditioning control system, which controls the temperature, humidity, and CO2. With this system, vegetables can be grown most anywhere in the world.
In the deserts of Port Augusta, Australia, Sundrop Farms operates a 49-acre indoor farm that produces 17,000 tons of fruits and vegetables. 180,000 non-GMO tomato plants, grown without soil, herbicides or pesticides supply 13% of all the tomatoes consumed in Australia.
Not everything can be grown in a vertical farm. Produce—like potatoes—don’t turn enough of a profit to make it worth growing indoors. Vertical farms usually stick to leafy greens and tomatoes, which grow quickly and can be sold at a premium on the market. Heavy crops like wheat and rice, which make up a lot of the American diet, aren’t feasible for vertical farms, as they require a lot more space and weigh more.
While vertical farms might also use a lot less water, they do require a lot of energy. In nature, sunlight is free. In a vertical farm, artificial lights add to carbon emissions at a much higher rate than traditional farms.
Urban sites for vertical farms are more expensive than open farm land. The cost of creating such a farm, installing the required lighting, and controlling the ambient temperature is not cheap. The cost to the consumer could cost them far more than what they now pay for outdoor farmed produce. Controlling the environment within these buildings with regards to lighting, temperature, pollination and the arrangement of plants will all be important factors for success.
Outdoor farmers always face the potential that their crop could be contaminated. Since vertically farmed produce are grown indoors, where they're always monitored and kept away from harmful bacteria, contamination is very unlikely. In an indoor vertical farm, everything that is happening can be controlled. The future of farming is not far away.
The content & opinions in this article are the author’s and do not necessarily represent the views of AgriTechTomorrow
Comments (0)
This post does not have any comments. Be the first to leave a comment below.
Featured Product
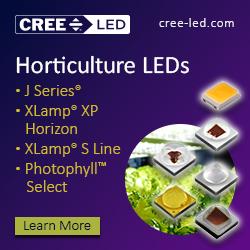