Forage Mass Monitoring (FFM) analysis has been traditionally done using biomass sampling to calculate biomass yield per hectare (t ha-1). Current research is now looking at reflectance spectroscopy methods using remote sensing systems based on unmanned aerial vehicles (UAVs).
Remote Sensing of Vegetation Using SWIR Cameras on a UAV
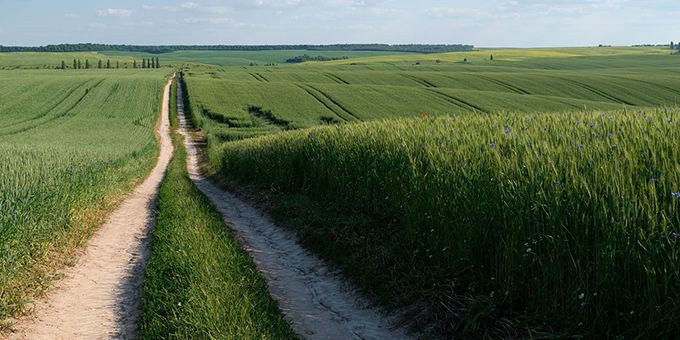
Case Study from | Raptor Photonics Ltd
Forage Mass Monitoring (FFM) analysis has been traditionally done using biomass sampling to calculate biomass yield per hectare (t ha-1). Current research projects are now looking at reflectance spectroscopy methods using remote sensing systems based on unmanned aerial vehicles (UAVs). Promising results in recent years prove the principal suitability of such systems for airborne monitoring of small to mediumsized farmland in agricultural applications for precision agriculture, such as biomass for crops and grasslands.
An imaging system in the form of a multispectral multicamera system is often used to derive well-established vegetation indices (VIs) efficiently. However, due to the use of silicon-based sensors, the spectral application range of such multi-camera systems is limited to the visible (VIS) and near-infrared (NIR) wavelength range (400-1000nm). Therefore, more robust indicators linked to biomass in the short-wave infrared (like cellulose or moisture content) cannot be considered as estimators.
Figure 1: Schematic system overview (See Ref [1])
In a joint research project, a team from the University of Applied Science Koblenz and the Remote Sensing and GIS group at the University of Cologne developed a UAV-based multi-camera system to collect NIR/SWIR data, to prove more robust and better-performing estimators of biomass monitoring. The system displayed in figure 1 shows a spectral camera unit (SCU) and a sensor management unit (SMU), both mounted onto a drone solution. The SCU deploys two Raptor Owl 640 M Vis-SWIR cameras enabling the coverage from 600 to 1700 nm of the electromagnetic spectrum. These camera modules were chosen because of their optimized “Size, Weight and Power” parameters. Thanks to the small form factor, the energy-efficient uncooled (TEC-less) design and the high sensitivity, these modules are ideal for integrating multiple camera modules into a lightweight, UAV-based remote sensing system for daylight operations. Another advantage is the interchangeable lens mount used for a custom filter flange solution to adapt application-specific narrow bandpass filters in the optical path.
Figure 2: Location and layout of the experimental site (see Ref [2])
The study aimed to validate the spectral performance and investigate spectral image data of a newly developed VNIR/SWIR multi-camera prototype for forage mass monitoring. For this purpose, aerial image data were acquired by the system on a permanent experimental grassland site near Cologne (chessboard trial), Germany, under clear sky conditions in July 2019. Spectral ground truth data were acquired with an ASD Fieldspec3 (FS3) spectroradiometer in twelve selected plots. Forage mass expressed in dry matter yield (DMY) was obtained by destructive biomass sampling 14 days after the flight date from all 156 trial plots.
Figure 3: Image data processing workflow.
To evaluate the VNIR/SWIR camera system’s spectral properties, the reflectance values of the individual spectral bands, and the two derived VIs, NRI (Koppe et al. 2010)3 and GnyLi (Gnyp et al. 2014)4 , were directly compared with the corresponding FS3 values. Moreover, the camera- and FS3-based VIs were further analyzed in simple linear regression models as estimators for DMY. The camera-based SLR resulted in an R2 of 0.71 to 0.75. These are promising results for a single flight date data set. However, further multi-temporal studies with advanced evaluation methods have to be carried out to confirm these results. Moreover, further estimation models for nitrogen concentration and crude protein content have to be evaluated. Evaluations for cereal crops are currently under investigation.
Ultimately, these first promising evaluation results demonstrate these novel InGaAs sensors’ suitability for use in multi-camera systems for UAV-based vegetation monitoring. They provide easy-to-use data with excellent spatial resolution in the selected wavelength bands over the entire spectral range from 600 - 1700nm.
References:
Ref [1] Jenal, A.; Bareth, G.; Bolten, A.; Kneer, C.; Weber, I.; Bongartz, J. Development of a VNIR/SWIR Multispectral Imaging System for Vegetation Monitoring with Unmanned Aerial Vehicles. Sensors 2019, 19, 5507, doi: 10.3390/s19245507.
Ref [2] Jenal, A.; Lussem, U.; Bolten, A.; Gnyp, M.L.; Schellberg, J.; Jasper, J.; Bongartz, J.; Bareth, G. Investigating the Potential of a Newly Developed UAV-Based VNIR/SWIR Imaging System for Forage Mass Monitoring. PFG – J. Photogramm. Remote Sens. Geoinformation Sci. 2020, 88, doi: 10.1007/s41064-020-00128-7.
Ref [3] doi: 10.1127/1432-8364/2010/0047
Ref [4] doi: 10.1016/j.jag.2014.05.006
Figure 4: Owl 640 M
• VIS-SWIR InGaAs technology | Enables imaging from 0.6μm to 1.7μm
• TEC-less Visible SWIR | Enables ultra low power
• Ultra-Low Noise Sensor: 18e- in High Gain | Enables ultimate low light Vis-SWIR image
• 15μm x 15μm pixel pitch | Enables the highest resolution SWIR image
• Ultra high intrascene dynamic range | Enables simultaneous capture of bright & dark portions of a scene
• Onboard Automated Gain Control (AGC) | Enables clear video in all light conditions
• Ultra compact, Rugged, Low power | Specially designed for integration into small OEM platforms
The content & opinions in this article are the author’s and do not necessarily represent the views of AgriTechTomorrow
Comments (0)
This post does not have any comments. Be the first to leave a comment below.
Featured Product
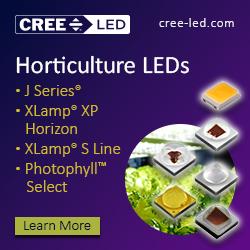