At the ETH Zurich, a robot has been developed to mechanically destroy the weeds growing between crops. “Rowesys” is conveniently started via remote control – and makes herbicides unnecessary.
Autonomous Field Worker
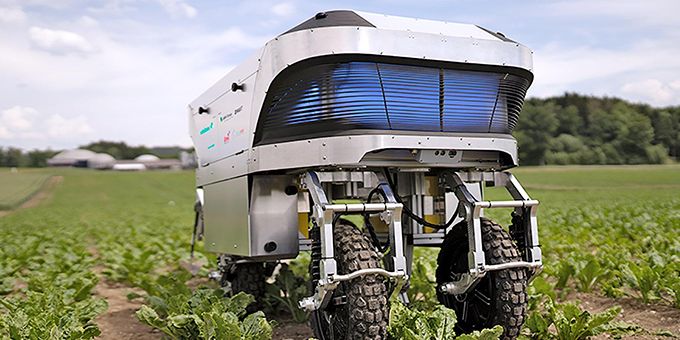
Article from | maxon group
Endangered species diversity. Overburdened ecosystems. Too much pesticide in the groundwater and in the air: The world urgently needs more sustainable agriculture. This transformation is possible, as proven by the growing number of innovative approaches – such as the Robotic Weeding System, or Rowesys for short, developed at ETH Zurich. This project shows that forgoing chemicals that kill weeds, fungi, and pests does not mean forfeiting profits. The prototypes of Rowesys are especially suitable for use in sugar beet fields, which require very intensive weed control. Whereas other solutions only concentrate on reducing pesticides, for example by means of more accurate spraying methods, the ETH robot makes the use of herbicides obsolete. It pulls the weeds out of the soil between the rows of plants, makes a turn at the end of the field, and continues along the next row. The autonomous robot can even handle mud or rocks in its path. Pascal Lieberherr, initiator of the project and a masters’ student in Robotics, Systems, & Control at ETH Zurich, became aware of the challenges in the food chain during his apprenticeship in food processing. Today, he is particularly interested in a key question: How can we feed humankind without burdening the nature of our planet?
Efficient cultivation
The team, which consists of mechanical and electrical engineering students from ETH Zurich and industrial design students from the University of Applied Sciences and Arts Northwestern Switzerland (FHNW), developed a robust locomotion concept. The vehicle is driven by four e-scooter hub motors that have a compact transmission, due to the small distances between the crop rows.
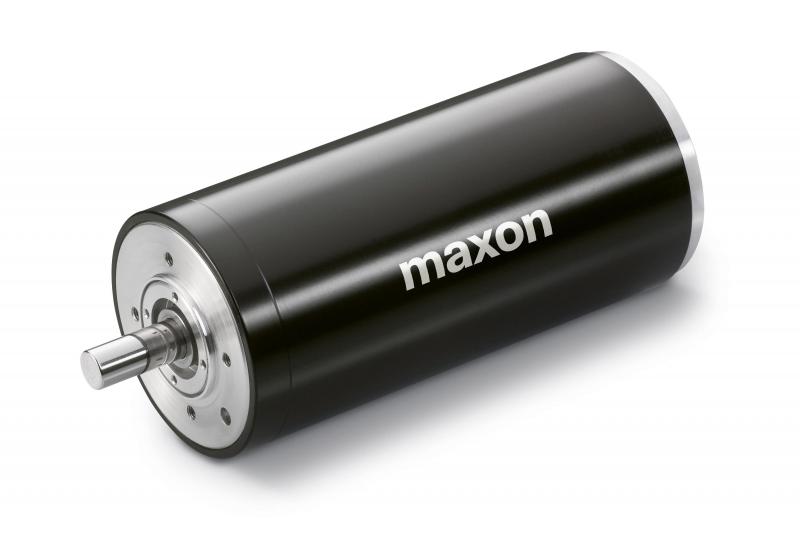
RE 50 DC motor
Each wheel axis of Rowesys can be rotated 180 degrees on both sides and is controlled by a drive unit that consists of an RE 50 DC motor with a GP 62 planetary gearhead for the speed reduction and an encoder. This motor offers high efficiency, is energy-efficient, and extremely powerful.
A mechanical spring-damper system ensures that the individually controllable wheels are always in contact with the ground and continue to work reliably even if the plowshares are immersed. This is important, on the one hand, because faulty operation would damage the crops and reduce the yield. On the other hand, the well-balanced weight distribution reduces localized soil compaction.
In addition to process reliability, user-friendliness was another aspect to which Pascal Lieberherr and his team gave high priority. As a result, Rowesys does not need GPS and can be conveniently remote-controlled. For a future version of the robot, it is planned that the robot will drive itself from the farmstead to the field and back again. Two powerful batteries ensure that an eight-hour shift is possible.
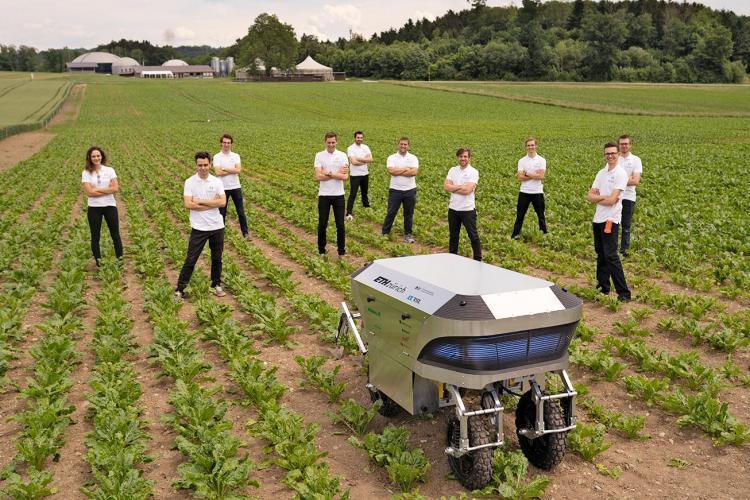
Wind, disease, and pests
Two visual sensors take care of navigation in the field. While the front camera detects the rows of plants, the one facing the soil distinguishes between weeds and crops. The software, which was programmed especially for this purpose, analyzes the images of the front camera for green areas and thus detects the direction of the crop row. It is planned to implement teachable software for analysis of the soil image. The purpose of this is to widen use of the software to other crops, such as corn.
Developing the software presented several challenges. One such challenge were the strong gusts of wind that blow the leaves into new positions within seconds. The system then has to immediately reinterpret the rapidly changing images and react accordingly. Work is still required in the area of detection of diseased plants, or those affected by pests.
The enthusiastic response to the project when it was presented in the summer of 2020 convinced Pascal Lieberherr that development of the intelligent agricultural robot is set to continue. In June 2021, the Agri-food Competition for Robot Evaluation (ACRE) will be held. This initiative is supported by Horizon, the EU Framework Program for Research and Innovation. Here, mobile robots for agricultural use will compete with one another, providing the perfect opportunity for Rowesys to show its strengths on the international stage.
The content & opinions in this article are the author’s and do not necessarily represent the views of AgriTechTomorrow
Comments (0)
This post does not have any comments. Be the first to leave a comment below.
Featured Product
