By using a computer vision-controlled system to map terrain and identify the size and location of rocks embedded in the soil, the heavy lifting is done by automated machinery which saves farmers a lot of time and money.
This Rocks: Terraclear's Rock-picking Robot Increases Productivity for Farmers
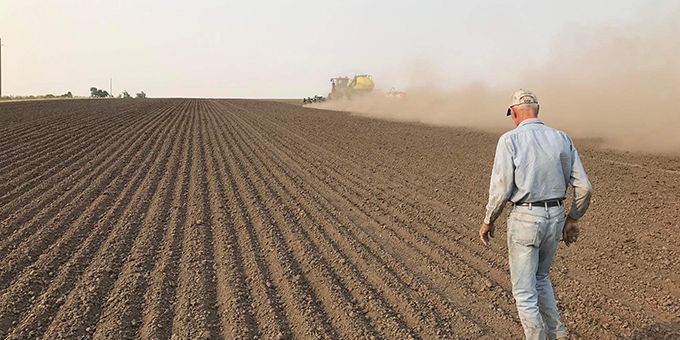
Case Study from | LUCID Vision Labs
Automation has become an increasingly critical factor in agriculture and smart farming over the last decade. By utilizing advanced technologies such as smart sensing, machine learning, and robotics, farming processes can be optimized in many innovative ways.
With a true mission to make farming easier and increase productivity, TerraClear is developing an end-to-end automation system which focuses specifically on automating rock removal. By using a computer vision-controlled system to map terrain and identify the size and location of rocks embedded in the soil, the heavy lifting is done by automated machinery which saves farmers a lot of time and money.
Challenge
Farmers deal with rocks and rock removal as they arise annually from tillage, frost heave, and weather impact. If not properly dealt with, rocks break equipment which can lead to costly fixes and substantial delays during the most critical windows of the growing season. Picking rock is often avoided by growers, as it is time-consuming, physically arduous, and perpetually frustrating, which is why most farmers agree that they should pick more rock, but simply do not make the time. Furthermore, with growing farm sizes and increased strain on labor markets around the continent, automating low-skilled tasks are increasingly important.

Existing solutions largely consist of mechanical rock pickers that churn through the soil to pull up rocks, and rollers that push the rocks back into the ground. The mechanical pickers can be effective, but they are very slow and can only be used in specific soil conditions. Therefore, most farmers either pick by hand (walking alongside a tractor/gator/skid steer and placing rocks in manually) or roll their fields. Rolling can be efficient, but in certain soil types has negative effects from compaction, and it typically only solves the problem for small rocks.
Solution
TerraClear is developing a Rock Clearance Solution that involves aerial mapping and on-the-ground automated picking. First, a drone conducts a survey using advanced sensors, GPS, and trained neural networks using computer vision to accurately map rocks’ locations and sizes. Then there is a hydraulically controlled implement mounted on a tractor or skid steer. A human then drives the tractor or skid steer on the optimized route provided by the map, and the computer vision on the implement automatically identifies the rock and pulls it into the tractor bucket.

The system uses multiple Triton 2.3 MP GigE PoE cameras from LUCID that capture high-resolution images that are used in three main areas: accurate training of neural networks, identification of rocks from aerial imagery, and real-time identification of rocks with the picking robot. According to TerraClear, the cameras need to be compact, lightweight and energy-efficient for use on aerial platforms and mobile machinery. They are mounted to TerraClear’s rock picker to identify the rocks in front of the tractor as it moves through a field. This is a critical step in the solution.

IP rated housing and M12/M8 connectors make the Triton cameras ideal for outdoor operation, withstanding regular exposure to the elements as the tractor or skid steer travels through dirt. In addition, the Triton’s shock and vibration resistance enables robust operation while mounted on farm machinery. For the picker to be able to identify and pick rocks, the cameras must capture high-quality images and high frame rate GigE video for accurate object tracking. LUCID’s active sensor alignment ensures precise object identification and tracking. In addition to these key camera specifications, TerraClear’s experience with LUCID’s Arena SDK and technical support has been very positive in the early stages of prototyping.
Conclusion
TerraClear’s solution can benefit farmers by providing the ability to clear farm fields of rocks efficiently and cost-effectively, and provide confidence that a high percentage of rocks have been found and removed. This considerably reduces damage to equipment and downtime risks during critical windows of farming.
The content & opinions in this article are the author’s and do not necessarily represent the views of AgriTechTomorrow
Comments (0)
This post does not have any comments. Be the first to leave a comment below.
Featured Product
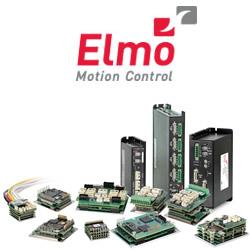