Polycarbonate panels offer growers a superior cladding solution, delivering effective light transmission and diffusion, simplifying maintenance and improving their structure’s heat retention. They also present a number of options to choose from.
Why More Growers Are Choosing Polycarbonate Panels
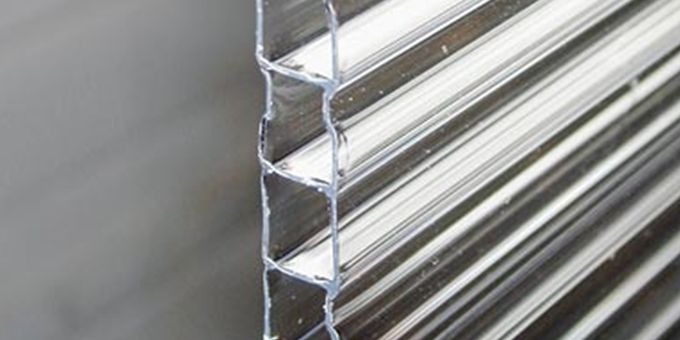
Article from | GrowSpan
In greenhouse crop production, an operation is only as effective as its structure’s cladding. To produce consistent, high-quality harvests year-round, growers need a cladding that will help create ideal conditions for their crops, regardless of the environment outside.
Along with improved plant growth, the best material will also limit monthly operating costs and help growers increase their bottom line. For these reasons, many greenhouse growers today are opting for polycarbonate panels to cover their structures.
Polycarbonate panels offer growers a superior cladding solution, delivering effective light transmission and diffusion, simplifying maintenance and improving their structure’s heat retention. They also present a number of options to choose from, which means operations in any region can use polycarbonate panels to improve their business.
WHAT ARE POLYCARBONATE SHEETS?
Polycarbonate panels are sheets made from rigid plastic that are nearly as transparent as glass. Their material offers sufficient impact resistance and creates one of the strongest greenhouse coverings available to growers.
In addition to superior strength, polycarbonate panels provide a greenhouse with high levels of both light transmission and light diffusion. An ideal range for light transmission in greenhouse production is typically considered between 80 and 90 percent. Polycarbonate greenhouse panels hover at both ends of that threshold, depending on their thickness and number of layers.
8 mm twin-wall polycarbonate offers a light transmission rate of around 80 percent. This allows most crops to thrive and mitigates the risk of them overheating or being scorched by excessive sunlight.
This is also the case with light diffusion. Crops generally grow better with diffused light, because it reaches all around them and is distributed more evenly. Polycarbonate panels employ diffused light to promote uniform crop growth and limit the amount of direct light that hits the top of crops. Too much harsh, direct light can potentially hinder crop development.
Polycarbonate greenhouse panels are designed to give growers a more convenient solution as well. They are shatter-resistant and virtually unbreakable, which simplifies transportation to sites, because the polycarbonate panels are less likely to be damaged during shipping. These sheets are also lightweight, so they can be easily cut and installed in larger sections, streamlining greenhouse construction.
HOW LONG DOES POLYCARBONATE LAST ON A GREENHOUSE?
Polycarbonate greenhouse panels are extremely durable and provide operations with a reliable covering that lasts years. In both single-layer and twin-wall, these polycarbonate panels are highly impact resistant, and feature a 10 year warranty.
This resistant polycarbonate is a cost-effective material that delivers high performance during its lifespan. To potentially increase life expectancy, growers can treat their polycarbonate panels with a UV protectant that helps prevent fading or discoloration.
The content & opinions in this article are the author’s and do not necessarily represent the views of AgriTechTomorrow
Comments (0)
This post does not have any comments. Be the first to leave a comment below.
Featured Product
