Although many of the currently available LED fixtures look similar and often utilize many identical components it is still important to fully explore performance metrics when evaluating lighting options.
4 Things To Consider When Comparing LED Lighting Systems
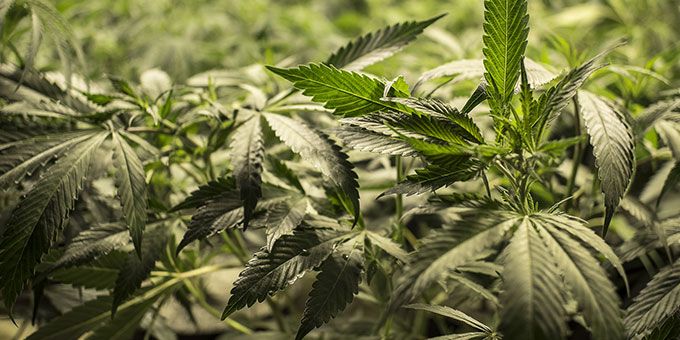
Mitch Galton | urban-gro
Broad-spectrum LED lighting solutions have become increasingly common for indoor horticulture and vertical farming applications in recent years. Although many of the currently available LED fixtures look similar and often utilize many identical components (such as brand-name LEDs or 645-watt power supplies), it is still important to fully explore performance metrics when evaluating lighting options.
Output
The first piece of information to consider when evaluating any LED solution will be the fixture’s total light output; photosynthetic photon flux (PPF). This metric -with units of µmol/s – simply describes the number of photons (which are “particles” of light) being produced by a fixture each second. Many vendors will list PPFD on spec sheets, but unlike PPF, this canopy light intensity metric will be affected by factors like fixture spacing, distance from the canopy, wall reflectivity, etc.
Understanding total fixture output / PPF will be the first step in accurately quantifying differentials among solutions. Increasing PPF will generally increase CapEx - but also often increase revenue through higher yield potential.
Efficacy
Once you’re confident that all lighting options being considered provide enough intensity to meet your production goals, the next metric to focus on will be efficacy; the amount of light being produced by each watt of electricity (with units of PPF / Watt). Efficacy is important to consider because it will directly relate to fixture wattage, sensible load for mechanical equipment, and ultimately OpEx from lighting. Because of differences in efficacy, two lighting options can have the same wattage & canopy coverage, but dramatically different light outputs. Similarly, two fixtures can have identical output, but very different electrical & sensible load requirements.
Spectrum
All photons also have an associated wavelength which we perceive as the photon’s color. While efficacy and PPF count all photons with wavelengths between 400nm-700nm, the spectral composition of light is also extremely important to consider for plant health. Broad-spectrum lights, which simply produce a relatively even distribution of red photons (600nm-700nm), green photons (500nm-600nm), and blue photons (400nm-500nm) are typically optimal for photosynthesis and canopy penetration, but not for efficacy maximization. As an example, red LEDs have the highest efficacy, but many cannabis cultivars experience photobleaching under high light intensity if the spectral composition contains over 50%-60% red photons. Red / blue photon heavy spectra also typically oversaturate surface photoreceptors which limits canopy penetration.
Form Factor (Uniformity)
Once you understand the outputs (photons/spectrum) and inputs (watts) of your fixture options, placement and form factor are important to consider. Raising the height of a fixture doesn’t reduce the number of photons being produced, but it spreads the same number of photons over a larger area. As a result, raising fixtures can be a valuable strategy to increase the uniformity of photons at the plant level – which will be essential to maintaining a consistent canopy and growth rate – but it also increases the likelihood of losing photons to walls / the floor.
In large rooms or greenhouse zones with rolling benches that create a constant canopy area, fixtures can be placed relatively high above plants. The fixtures at the edge of these large areas will still lose photons to the floor/walls, but the majority of lights will be closer to the center with nearly all photons reaching plants. The large footprints of each fixture will overlap to increase PPFD. Because of the mounting height in this setting, operators could deploy compact high output fixtures with relatively sparse placement while maintaining uniformity.
By comparison, a producer running 4’ wide canopy sections with static aisles would benefit from bringing lights as close to plants as possible to reduce spill over into the aisles (where photons won’t drive plant growth/revenue). To maintain uniformity of photons at canopy with the closer proximity, this cultivator could deploy larger fixtures with a more spread-out light emission surface.
About urban-gro, Inc.
urban-gro, Inc.® (Nasdaq: UGRO) is a global engineering and design services company focused on the commercial horticulture market. With experience in hundreds of Controlled Environment Agriculture (CEA) facilities spanning millions of square feet, we engineer, design and integrate complex environmental equipment systems into high-performance facilities. Once operational, urban-gro’s gro-care® Managed Services Platform leverages the company's expertise to reduce downtime, provide continuity, and drive facility optimization. Operating as a crop-agnostic solutions provider in both food and cannabis CEA sectors, our crop-focused end-to-end approach provides a single point of accountability across all aspects of growing operations. Visit urban-gro.com to discover how we help you gro plants and gro profits.
The content & opinions in this article are the author’s and do not necessarily represent the views of AgriTechTomorrow
Comments (0)
This post does not have any comments. Be the first to leave a comment below.
Featured Product
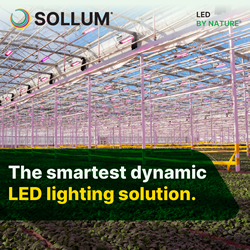