At C.J. Moyna & Sons, being on the lookout for disruptive technologies is a part of his everyday routine. When they set on a path to integrate additive manufacturing into their daily processes, the work became easier for C.J. Moyna & Sons and their sister companies.
How 3D Printing is Paving the Way for Grading Contractor, C.J. Moyna & Sons
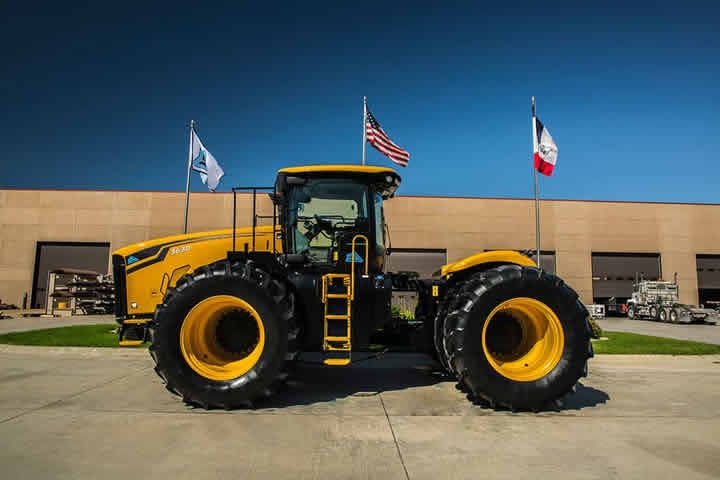
Case Study from | BigRep
The heavy civil construction sector (e.g. highway road construction, mass excavation) is literally heavy-handed when it comes to engineering and manufacturing new components. The bottleneck is that it takes an eternity with conventional methods to materialize these parts.
For Ryan Young, a project manager at C.J. Moyna & Sons, being on the lookout for disruptive technologies is a part of his everyday routine. When they set on a path to integrate additive manufacturing into their daily processes, the work became easier for C.J. Moyna & Sons and their sister companies.
Founded in the 1940s, C.J. Moyna & Sons is a family-run business that has shaped the landscape of Iowa for three generations ever since. The company specializes in civil earth moving, equipment manufacturing, and aggregate processing & mining and belongs to the premier grading contractors in the Midwest.
However, the pandemic presented the company with major challenges. With the global supply chain being disrupted, the company needed to find a way to meet its demand for components.
Especially, for the Earthmoving Legacy Center, where the owner John Moyna exhibits historical construction vehicles, it was impossible to find spare parts for antique caterpillars, tractors, and scrapers.
The Earthmoving Legacy Center is a 38000 square foot facility to showcase the rich history of earthmoving.
Young and his team found a compelling solution with additive manufacturing that became a game changer. When C.J. Moyna & Sons first tried out some hobby 3D printers, it became evident that an industrial large format printer with an open material system would be a better fit.
Ryan Young, a project manager with an exhibit at the C.J. Moyna & Sons legacy center.
For Ryan Young, the BigRep PRO checked all the boxes – the massive build volume, accuracy, reliability, and the entire 3D printer ecosystem the company offered sealed the deal.
Patrick Palmersheim, System Administrator, uses the BigRep PRO to restore parts of the construction vehicles in the legacy center which are pretty much impossible to find anymore. Thus, the company’s heritage is being cared for and kept alive. Palmersheim also praised BigRep’s engineers who helped him solve smaller issues.
C.J. Moyna & Sons doesn’t strictly use the BigRep PRO for restoration. Ryan Young says that they use it for rapid prototyping which supports sister company Mobile Track Solutions, for manufacturing mock-ups, functional dash parts, and final parts.
For the R&D team, the PRO prints functional dash parts in a couple of days. E.g. with the injection molding process, it would have taken weeks or months.
“In 2 or 3 days you can have a large functional piece printed by the BigRep PRO – ready to rock and roll.”
Speaking about the filament, Ryan Young likes the fact that the BigRep PRO prints with materials from different brands which makes the industrial 3D printer versatile. His favorite filament is the PRO-HT – a biopolymer with reduced environmental impact which is easy to print, FDA compliant for food safety, and formulated for effortless breakaway support removal.
After the printing process, the rapid innovation manager says some post-processing is needed, but “a lot of time the parts are in a good shape when they come out the printer.”
Driving the Future
For Paul Palmersheim, it’s been a really great experience working with BigRep. And for Young? He says it’s had “a tremendous impact” on how they are manufacturing and looking towards the future of engineering. From his point of view, 3D printing will be growing and improving in the future. And his prediction: “I can see in another 10-15 years, 25-30% of parts are gonna be 3D printed.”
The content & opinions in this article are the author’s and do not necessarily represent the views of AgriTechTomorrow
Comments (0)
This post does not have any comments. Be the first to leave a comment below.
Featured Product
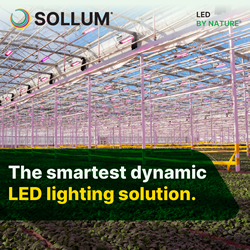