Localized CO2 monitors, placed in close proximity to the plants themselves would help combat microclimates forming within the growing areas, which are liable to change as plants grow and mature.
Maximizing Commercial Greenhouse Yields Through CO2-Sensing IoT Systems
Neill Ricketts, Chair | GSS
The use of automation to improve yields in commercial greenhouses has accelerated rapidly in recent years, with nutrients, water, temperature and lighting all tightly controlled by sophisticated IoT systems taking data from local sensors and climate computers to optimize growing conditions. Advances in these IoT systems have concentrated on efficiency to reduce operational costs for the farm while maximizing yield.
Of course, missing from the above list environmental factors is the regulation of the greenhouse’s CO2 concentrations. Obviously, the gas is needed for photosynthesis, but too high a concentration can damage the plants.
Localized CO2 monitors, placed in close proximity to the plants themselves would help combat microclimates forming within the growing areas, which are liable to change as plants grow and mature.
IoT sensors
While CO2 sensors exist, and therefore could be used in an IoT system, a key limitation in their use is their power consumption. Given the nature of greenhouses, which cover large areas and have power directed to lighting and heating rigs rather than to power sockets, IoT systems would need to be battery operated to enable them to be moved easily, but traditional sensors use incandescent light sources to detect the gas concentrations use too much power.
Like all gases, carbon dioxide absorbs light at specific wavelengths, in its case the mid-infrared (IR) wavelength of 4.25 µm. Traditionally, gas sensors use incandescent IR light sources to illuminate a gas and measure the absorption spectrum to understand each gas present (see figure 1). However, these incandescent sensors require significant levels of power to operate and this has limited their use to mains powered IoT equipment only.
Fig 1: Airborne substances can be identified by their absorption of IR at specific wavelengths. The above show the absorption spectrum for several chemicals found in the air, including CO2, NOX and methane.
Sensors are moving away from incandescent IR emitters, with solid-state LEDs and emitters now being used. Like elsewhere, these offer the lowest power consumption and longest mean time to failure. And these non-dispersive infrared (NDIR) solid-state sensors are significantly more power efficient than incandescent light sources but even in these, the power consumption is typically in the region of 50 to 150 mW average, with a peak of 300-400 mW.
This is still too high and battery-powered IoT systems would either require regular battery changes or be limited to systems designed for short-term use only, for example implementing a rechargeable Li-ion battery and using it to test specific areas of concern only. This latter case is not ideal, and the man hours needed to regularly check and replace batteries would be prohibitively expensive.
A more power efficient design
Significant energy savings are, however, possible.
Fig 2: The GSS CoziR-Blink uses an alternative topology to significantly reduce power consumption. When the sensor is switched on, a measurement is automatically initiated. Data can be read out once the READY pin is pulsed high, approximately 3.3s after application of power. The sensor can then be subsequently switched off, saving power.
The sensor’s biggest power drain is the light source and therefore reading frequency matters. Were this a carbon monoxide or radon detector then it would need to run several times per second, but greenhouses are not safety critical environments and carbon dioxide is not directly toxic to either the plants or the workers in concentrations that will be normally present, so sensors can be set to run at far less frequent intervals.
If we therefore adjust the duty cycle and have it run at a much lower frequency it is possible to bring power consumption down significantly. CO2 rises will happen slowly, and the concentrations needed to build up plant damage from high concentrations – even in microclimates around the plant - will take several hours, so for in-greenhouse applications, every 10-15 minutes will be well within the plants’ tolerated thresholds.
Processing is the next biggest power drain and efficiency gains can be made here through the optimisation of signal processing algorithms used by the sensor, as well through the use of measures (especially hardware) adopted to reduce computational loads.
And measures can also be taken to reduce the power used during stand by, with sleep modes implemented as well as the incorporation of more energy-efficient components elsewhere on the board.
Combined, these elements can make it is possible to create a more efficient CO2 sensor.
IoT system development
These advances show that, by adapting solid-state LED sensors and making changes to the duty cycle, implementing more efficient algorithms, and considering the power consumption of every on-board component it is possible to reach the power levels required for greenhouse CO2-sensing IoT systems.
Fig 3: A schematic for an IoT CO2 sensor for use in air quality monitoring. Switching to the new generation of low-power CO2 sensors, with an appropriately set duty cycle, would enable this to run for years before batteries are replaced.
A wireless CO2 sensor suitable for use in such a system needs to consists of four major building blocks, the CO2 sensor, microcontroller, low power radio module and a power source (see fig 3).
Sensor: As we’ve highlighted, advanced sensors can run at 60 µJ per cycle, with just four to six cycles per hour.
Wireless data transmission protocol: For this, LoRaWAN is arguably the best suited protocol as it can be both exceptionally power efficient yet can transmit over the very large area of a commercial greenhouse complex without the need for multiple routers.
The processor: A microcontroller with a low power design and exceptionally-low-power sleep mode will be needed and a good example of this is the STM32L0 from ST Micro.
And this leaves the power source. The above combination of components within an IoT system will be able to run for several years when powered by AA batteries. However, the IoT system will also be within the range of energy harvesting, with solar panels powered by both the sun and any lighting rigs enabling them to run indefinitely.
Neill Ricketts is the chair of the ultra-low-power CO2 sensor developer, GSS.
The content & opinions in this article are the author’s and do not necessarily represent the views of AgriTechTomorrow
Comments (0)
This post does not have any comments. Be the first to leave a comment below.
Featured Product
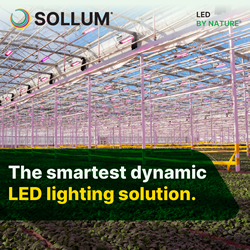