Compass Wire Cloth: The Crucial Role of Screen Quality in Industrial Processes
Compass Wire Cloth highlights its line of wire cloth screens and their capabilities. From food production to aerospace applications, the performance and reliability of wire cloth screens directly impact the quality, safety, and efficiency of production processes. This article explores the nuances of screen quality, its far-reaching effects on product outcomes, and how businesses can leverage high-quality screens to enhance their operations.
The Crucial Role of Screen Quality in Industrial Processes:
By Christopher Toppi, VP of Sales & Operations; David Gentilini, National Account Executive
In the world of industrial manufacturing, screen quality plays a pivotal role in determining product consistency and operational safety. From food production to aerospace applications, the performance and reliability of wire cloth screens directly impact the quality, safety, and efficiency of production processes. This article explores the nuances of screen quality, its far-reaching effects on product outcomes, and how businesses can leverage high-quality screens to enhance their operations.
The Relationship Between Screen Quality and Product Consistency
At its core, screen quality governs the precision with which particles are sized and sorted. Whether it's ensuring uniform particle size in food processing or meeting strict specifications for aerospace materials, a screen's weave pattern, material composition, and structural integrity are critical. Screens with poor quality or inconsistency in their weave can result in undersized or oversized particles, leading to out-of-spec materials. This not only compromises the end product but also necessitates costly rework and can damage customer relationships.
Safety Implications of Compromised Screens
Beyond consistency, screen quality has direct safety implications. For instance, in food processing facilities, broken screens can release fragments into the production line. Consider a hypothetical scenario involving a cereal manufacturer: if a standard stainless steel T304/T316 screen breaks, metal fragments could potentially end up in the product, going undetected. In this case, using T430 stainless steel would be a possible solution due to its magnetic characteristics, which would allow broken or loose wire fragments to be removed from the product.
In environments where dust, heat, and friction converge—common in industries handling powdered materials—screens may be equipped with grounding wires to prevent static discharge and potential explosions. Neglecting this precaution, whether due to poor screen quality or oversight, can lead to catastrophic workplace incidents.
Key Determinants of Screen Quality
Several factors determine the quality of a wire cloth screen:
-Material Composition: The alloy used, such as stainless steel types 304, 316, or magnetic 430, influences
a screen's resistance to corrosion and its ability to withstand environmental stresses. For instance, a
salt-processing facility (typically or may) requires highly corrosion-resistant materials. In many cases, t ype 316 may satisfy this requirement, but in some extreme environments Inconel alloys, which are highly
corrosion resistant and can withstand high temperatures up to 1800 degrees F, are used to maintain
operational integrity.
-Weave Precision: Consistent weaving ensures uniform openings, critical for particle size accuracy. The
ASTM E2016-22 Standard Specification for Industrial Woven Wire Cloth provides specifications for wire
cloth quality, enabling manufacturers to maintain consistency and traceability from raw material
sourcing to finished product delivery.
-Traceability: High-quality manufacturers implement robust traceability protocols, allowing them to track
materials from their origin at the mill to the final fabrication. This transparency not only assures quality
but also enables quick identification and resolution of issues if they arise.
Operational Efficiency and Long-Term Cost Benefits
Investing in high-quality screens is not merely a question of compliance or product excellence—it's also a strategic decision with long-term benefits. Superior screens often outlast their lower-quality counterparts, reducing downtime and its associated costs. For businesses where material costs and operational disruptions are significant, preemptive maintenance based on known screen lifespans can save both time and money. For example, a facility that replaces screens every five to six days, despite a seven-day expected lifespan, minimizes the risk of unplanned downtime—a critical consideration for industries dealing with expensive raw materials.
Moreover, feedback from customers underscores the efficiency gains achieved with premium screens. Reports of increased throughput and longer operational life demonstrate the tangible benefits of choosing quality over cost-cutting alternatives.
Preventative maintenance is the cornerstone of maximizing screen performance. Businesses should adopt regular inspection schedules to ensure screens remain taut and free of defects such as sagging, plugging, or broken wires. These checks not only extend the lifespan of screens but also maintain product quality by preventing issues like oversized material bypass or product contamination.
Maintenance teams can employ lab sieves to monitor for inconsistencies, enabling early detection of potential problems on the production floor. By addressing issues such as screen blinding—where clogged openings reduce material throughput—businesses can maintain operational efficiency and avoid costly rework.
Identifying the right time to replace a screen is vital. Signs such as reduced tension, visible damage, or inconsistent product results during lab tests indicate the need for replacement. In industries where downtime equates to substantial financial loss, proactive replacement strategies often prove more cost-effective than reactive measures.
Choosing the Right Partner for Screen Solutions
In conclusion, the quality of screens in industrial processes is not merely a technical consideration but a critical factor that directly impacts product consistency, safety, and operational efficiency. As industries continue to evolve and face increasingly stringent quality standards, partnering with a reliable screen solutions provider becomes paramount.
Companies like Compass Wire Cloth exemplify the kind of partner that can make a significant difference in industrial operations. Their commitment to quality assurance, with ISO 9001-compliant processes and full traceability, provides businesses with the confidence needed in today's demanding manufacturing environment. By offering customized solutions tailored to specific industry needs, from corrosion-resistant alloys for harsh environments to specialized features like grounding wires for dust-prone settings, they demonstrate the importance of adaptability in screen manufacturing.
Moreover, the value of a screen solutions partner extends beyond the product itself. Technical expertise, preventative maintenance strategies, and proactive replacement schedules are crucial services that can help businesses optimize their operations, reduce downtime, and ultimately improve their bottom line. The ability to respond quickly to urgent orders and provide ongoing support reflects a customer-first philosophy that is essential in building long-term partnerships.
As industries continue to face challenges in maintaining product quality, ensuring safety, and improving efficiency, the choice of a screen solutions partner becomes increasingly critical. By prioritizing screen quality and selecting a partner that offers comprehensive support, businesses can position themselves for success in an ever-competitive industrial landscape.
Featured Product
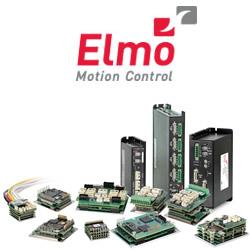
Elmo Motion Control - The Platinum Line, a new era in servo control
Significantly enhanced servo performance, higher EtherCAT networking precision, richer servo operation capabilities, more feedback options, and certified smart Functional Safety. Elmo's industry-leading Platinum line of servo drives provides faster and more enhanced servo performance with wider bandwidth, higher resolutions, and advanced control for better results. Platinum drives offer precise EtherCAT networking, faster cycling, high synchronization, negligible jitters, and near-zero latency. They are fully synchronized to the servo loops and feature-rich feedback support, up to three feedbacks simultaneously (with two absolute encoders working simultaneously). The Platinum Line includes one of the world's smallest Functional Safety, and FSoE-certified servo drives with unique SIL capabilities.