Iron Ox Announces Phil: The Next Robot In The Company’s Proprietary Greenhouse System
Iron Ox, a farming innovation company with deep expertise in plant science, robotics and artificial intelligence, has officially announced its second ground-breaking greenhouse robot, Phil.
Phil is a critical addition to the Iron Ox ecosystem that optimizes plant yield, expands growth cycles and maximizes crop quality. His state-of-the-art sensor technology identifies trends in each module’s water and nutrient mix, measuring nutrient content and pH levels with speed and precision. Phil is equipped with Ultraviolet LEDs for quick and efficient sanitizing without producing waste. The result is delicious, nutritious, locally sourced fruits and vegetables with substantially lower environmental impacts.
“The clever thing with Phil is that we can adjust each of the thousands of modules in our Texas greenhouse to grow the same and/or a variety of crops under different nutrient profiles, which in our controlled environment, rapidly accelerates our understanding of plant science,” said Brandon Alexander, Iron Ox CEO, who grew up picking cotton, potatoes and peanuts on his family’s farm in Texas. “This not only allows our grow team to optimize for the market demand, while giving each and every plant exactly what it needs — eliminating waste, but ultimately this knowledge can and will benefit the entire industry”
Phil is integrated into the Iron Ox greenhouse system, with all the data he collects going into the company’s robust agricultural dataset. This data informs the plant scientist’s optimization strategies. For example, when Grover brings a module in for a checkup, the amount of water and nutrient content may vary based on different conditions, and the team may see a trend that provides valuable information on water or nutrient usage for each plant varietal.
How it works
Phil quickly and precisely fills each 6-by-6-foot plant module in under two minutes. How it works: Grover, the recently announced autonomous mobile robot, transports plant modules and docks with Phil, who, using his advanced sensors, hygienically fills it precisely to the required volume and nutrient mix. The module is now ready for Grover to retrieve it and deliver it to its next destination. Phil enables high throughput of modules, making the interaction between Grover and Phil akin to a Formula 1 pitstop. This contactless procedure eliminates the need to re-sanitize Phil after each module.
“The addition of Phil enables fast throughput of plant modules in an efficient and food-safe process,” said Sarah Osentoski, Iron Ox Senior Vice President of Engineering. “Phil’s advanced sensors give the teams of plant and data scientists valuable information to optimize the entire closed-loop system of Iron Ox’s greenhouses.”
In addition, Grover brings Phil modules for checkups throughout each plant module’s growth cycle. Phil first takes a small sample of the water and nutrient mix. That sample goes into a reservoir equipped with sensors to measure the nutrient content and pH of the module. Iron Ox’s plant science team uses these data to understand how the plants are consuming water, and the nutrients and at what rate.
Phil then senses the water level and adjusts it to match its target settings. Another sample is taken for validation. When Phil is done with his work, Grover takes the plant module back to its respective place in the greenhouse.
Phil is yet another asset in Iron Ox’s closed-loop proprietary system that uses artificial intelligence, machine learning, robotics, and hydroponics to make the global agriculture sector more efficient, and robust while decreasing greenhouse gas emissions and other negative environmental impacts. The company’s technology currently produces a wide variety of crops, including herbs and lettuces, while using a small fraction of the land, water and energy compared to food grown on conventional farms.
Iron Ox plows through to hyper growth mode
Iron Ox operates farms in Northern California and earlier this year broke ground on the 535,000 square-foot indoor farm in Lockhart, Texas. The company is significantly scaling up, with its robotics fleet working alongside an expanding team of plant scientists, growers, roboticists and data scientists.
Iron Ox produce can be found throughout California at Whole Foods Markets and at San Francisco Bay Area markets such as Bianchini’s and Mollie Stone’s. Sales outside of California are expected to begin by the holidays with the first harvest from the new Texas facility.
This fall, Iron Ox announced a $53 million Series C funding round led by new investor Breakthrough Energy Ventures, an investment group backed by many of the world’s top business leaders and dedicated to achieving net-zero emissions by 2050.
Iron Ox is using this latest funding round to expand its intellectual property portfolio in robotics and artificial intelligence. The company is accelerating its efforts to hire plant scientists, engineers, greenhouse operators and roboticists to join their dynamic team. To learn more about careers at Iron Ox, please click here.
About Iron Ox
Based in California's Silicon Valley, Iron Ox is an agriculture technology startup with deep expertise in plant science, robotics and artificial intelligence. The company's mission is to make growing fresh produce carbon negative. Iron Ox has redesigned every step of the farming process, from seed to store shelf, achieving levels of precision that are impossible through conventional farming. Iron Ox produce is delicious, nutritious, sustainable, and local, greatly reducing food waste and reducing the environmental impacts of farming. For more information, visit www.ironox.com.
Comments (0)
This post does not have any comments. Be the first to leave a comment below.
Featured Product
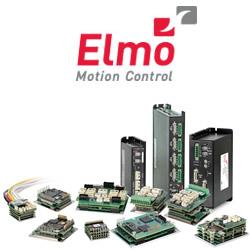