Robotics Engineers Work to 'Bee' Part of the Climate Change Solution
This summer’s weather extremes were stark reminders that climate change is not only real, it’s here. Less visible to most of us than smoke-filled skies, water-logged roads, and life-threatening heat—but just as important—is the dramatic and ongoing decline of global bee populations.
Many crops rely on commercially managed honeybees, wild native bees, and other pollinators to reproduce. In fact, one-third of every bite of food we eat comes from plants that need to be pollinated, so pollinator health affects all of us. But almost 35 percent of insect pollinator populations worldwide are at risk of extinction and more than half of North American native bee species are declining due to pesticide use, habitat loss, climate change, and intensive farming practices.
These concerning trends are at the root of the increasingly mainstream global campaigns to save the bees. But Nitin Sanket, an assistant professor in the Department of Robotics Engineering, is approaching this issue from an entirely different angle.
“A lot of conservationists are working to preserve bees, and that’s a good thing,” says Sanket, who joined WPI’s faculty in 2022. “But the climate is changing pretty drastically, so we need alternatives as well, including looking at other ways to pollinate things.”
Behold, the robo bee.
It’s an autonomous flying robot that Sanket and his graduate students in the Perception and Autonomous Robotics Group are developing with potential funding coming from a variety of sources, including military and environmental organizations. The current prototype is a small, 3D-printed black plastic cube that’s outfitted with four 2.5-inch propellors, a powerful camera, and a rechargeable lithium battery.
The existing model is 4.7 inches across—about the size of a hummingbird—but at 200 grams weighs about 100 times more than those feathered pollinators. It can quietly whir through the air while darting to avoid obstacles and turning to navigate narrow spaces, flying for a total of 5 to 7 minutes, depending on the type of battery it has and the type of movements it makes.
Sanket’s long-term goal is to create a device that’s small enough and contains enough power to fly independently in a swarm for many hours. The programming will be sufficiently sophisticated and nuanced so that the bot can successfully collect and transfer pollen from a variety of plants. Bonus points for the planet if the robotic bee could also run completely on solar power and fully biodegrade into the soil when its parts wear out.
Small Bug, Big Effort
Sanket cautions that he’s still many years away from a fully functional and green robotic bee, but he’s optimistic—in large part because engineers and researchers at other institutions are working on details that will no doubt help advance his project. Researchers at MIT, Harvard, and the University of Washington are tackling the mechanical challenges necessary to build a robotic body no larger than a bee. Meanwhile, in partnership with Yiannis Aloimonos and Cornelia Fermüller at the University of Maryland, Sanket’s team is perfecting the robot’s ability to smoothly and autonomously navigate around objects. In other words, they are building the robo bee’s brain.
But, notes Sanket, “You cannot use the same logic as you would for a human brain. And, obviously, we cannot probe into what bees are thinking. So we’re speculating.”
That speculation builds on existing entomological research into insect movement and behavior. Understanding how bees usually respond in specific situations helps Sanket and his team identify the many individual functions they need to program into the device’s cognition and autonomy.
Each of the two doctoral students and eight master’s students working with Sanket is tackling a different detail of the device. Specifically, they are trying to improve the robotic bee’s agility, speed, flight longevity, awareness of objects, and ability to avoid crashing into objects.
Robotics engineering master’s student Rishabh Singh is focusing on making the device fly faster while maintaining all of its current computing power and autonomy. He started working on the robo bee project a few years ago during an internship at the University of Maryland, where Sanket was an assistant clinical professor and postdoctoral researcher in computer science. Singh was the one who actually built the physical drones that Sanket flew during his postdoctoral research, and he came to WPI so he could continue studying with Sanket.
“This project is building on what we did at Maryland by adding speed, which adds a layer of complexity,” says Singh. “How can we get drones the size of a bee to fly autonomously through a forest at 30 meters per second? That’s three times as fast as the fastest autonomous drone right now.”
To fly that fast in that environment, the device has to be both lightweight and sturdy enough to carry the sensors needed for autonomous flight. In addition, “it has to be strong because it’s going to take a beating,” Singh says.
That’s because “real bees always run into each other,” Sanket explains. “They’re very clumsy. But that’s okay because their bodies are resilient.” Every time the current iteration of robotic bee runs into something, though, expensive machinery can break. Those laboratory crashes can offer valuable learning opportunities that, ultimately, should help Sanket and his team build a better robotic bee.
Fun Idea, Serious Impact
None of these details factored into Sanket’s thinking when he first began working on this project during his own time in graduate school.
“It started as a joke, to be honest with you,” says Sanket. One day, while talking with his advisor, he glanced at a tiny, squishy toy on his desk. “I said, ‘I should build a drone that small just to show that it’s possible.’ And once we actually started thinking about it, we realized it was not only a really hard problem to solve, but also one that could have a real impact.”
Sanket’s doctoral dissertation on robotic bees earned him awards at the University of Maryland and MDPI, an international publisher of open-access peer-reviewed scientific journals. He has been the lead author on several papers examining specific functions related to autonomous aerial navigation. Most recently, the August 2023 issue of Science Robotics featured on its cover a paper by Sanket and researchers from the University of Maryland showing that a robot’s ability to understand when assumptions may be incorrect is especially important in navigating unpredictable situations.
Once he’s able to perfect the tiny robot’s ability to maneuver in tight spaces and avoid other moving objects, Sanket knows the device could be valuable in a number of real-world situations that have nothing to do with plants or pollination, including search and rescue efforts. That possible use earned Sanket funding from the Office of Naval Research during his doctoral studies, and he’s now applying for new military grants. And while he is also talking with potential funders that focus on environmental issues, he isn’t worried that developing robotic bees will divert money away from widespread conservation efforts.
“This is bringing in new money, because people who would not invest in conservation might invest in this technology,” Sanket says. “It’s like when GPS was first developed by the military. They were interested in the technology for a completely different reason than what we’re all using it for today. But if they put in the money to develop a technology, then the general public can adapt that technology for creative solutions.”
In the meantime, Sanket and his students are steadily inching toward their goal of a fully autonomous bug-size device. They know that lives around the planet may depend on it.
Comments (0)
This post does not have any comments. Be the first to leave a comment below.
Featured Product
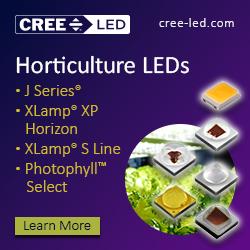