Ivy Tech Precision Ag Program prepares students with newest technologies in agriculture
Vineyard Robot Prototype to Debut at FutureFarm Expo in Oregon
Shenandoah Growers Deploying Indoor Farming Nationwide
Dealers Expecting Growth in Precision Farming Activities
These kale farming robots in Pittsburgh don't need soil or even much water
Roomba Inventor Joe Jones on His New Weed-Killing Robot
Getting creative to fix precision equipment glitches
Precision Farming Increases Crop Yields
'Near-zero-power' temperature sensor could make wearables, smart home devices less power-hungry
Rapid Change And Constant Disruption Demand A New Approach To Innovation
This quiet agricultural 'moonshot' could change the future of food
The 25 Most Innovative Ag-Tech Startups
Infarm wants to put a farm in every grocery store
Wells Fargo Awards $300,000 to THRIVE's AgTech Innovation Platform
Australia - New network to boost farm tech capabilities
Records 811 to 825 of 851
First | Previous | Next | Last
Featured Product
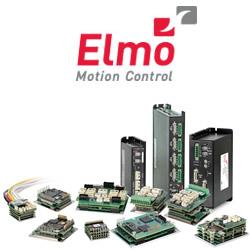